As we experience the hottest summer in years, a critical debate is unfolding around New…
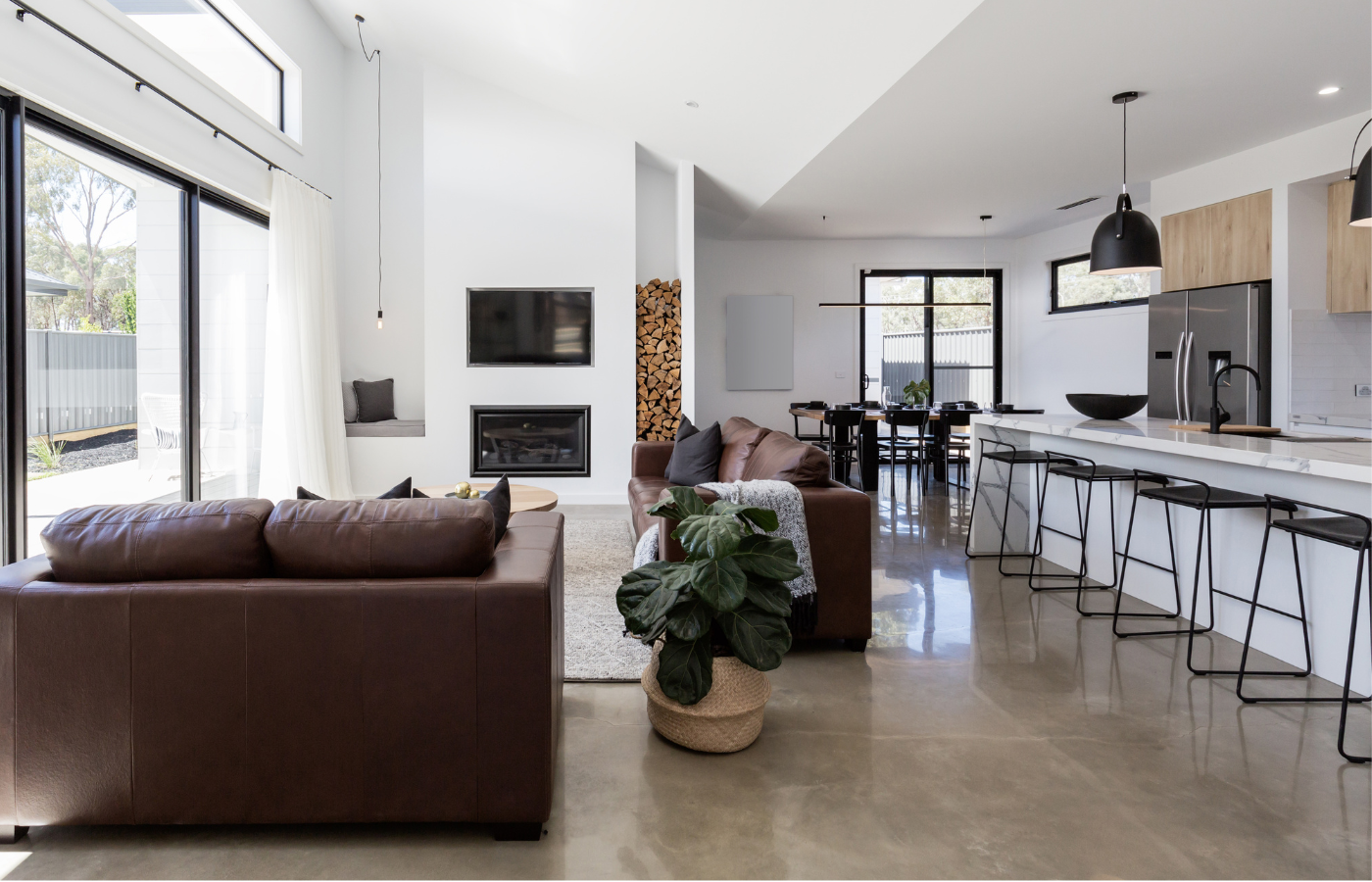
New approaches for meeting the H1 insulation requirements of concrete slabs
Perhaps one of the biggest impacts from the new H1 changes has been the effect on concrete slabs. The minimum R-value has increased across the board, with colder parts of the country seeing even larger lifts. Quite rightly, the new requirements recognise that concrete slabs are an important piece of the insulation puzzle. Responsible for up to 10% of a building’s heat being lost, insulating concrete slabs improves the comfort of the building, reduces condensation and lowers energy costs. Yet, while the R-value changes make great sense, making sense of what they mean for insulation requirements in practice is a little less clear.
How has the calculation for concrete slab R-values changed?
Concrete slabs requirements now take into account their area to perimeter ratio to determine the insulation required. This means that not only do buildings now require a higher R-value, it also takes more to achieve that value.
In response and almost overnight, architects and builders have needed to change the way they construct concrete slabs. This is especially the case in the warmer parts of the country, where previously, insulation was not always included in the concrete slab construction process.
Meeting the requirements
In order to meet the new insulation standards, the two approaches for architects and builders to increase the R-value of the slab are:
- Lay insulation under the slab
- Use perimeter insulation, attaching insulation to the edges of the slab
For even higher R-values, both approaches may be needed.
Underslab insulation
Underslab insulation is used on the prepared site, sitting on top of the waterproof membrane, and with the concrete slab poured over the top. For this reason, underslab insulation is not appropriate for retrofit solutions. In choosing the right material for underslab insulation, thermal efficiency, moisture resistance, product longevity and compressive strength are important considerations.
The thermal resistance properties of extruded polystyrene (XPS) have made this a good choice for underslab insulation in the past. However, in recent times, as supply chain issues have impacted the construction industry, getting XPS supplies onto our shores in a timely and consistent way has become increasingly more difficult. In addition, the cost of the product has also increased.
In response, EXPOL has invested in creating a product for the New Zealand market to match and exceed the performance of XPS. SLABX200 is the result of many years of experience and research. Using our own secret recipe, SLABX200 has been engineered to provide both a high R-value and an impressive compressive strength. SLABX200 also demonstrates high water resistance, and has a 20 year product warranty. SLABX200 can be used for slab on ground or waffle pod slabs.
In addition, SLABX200 is highly cost effective, made in New Zealand, and can be easily recycled into other EXPOL products. Note: it is important for specifiers to specify SLABX200 to ensure their clients receive the specific benefits of using this product.
Needing more or something different?
There are times when underslab insulation isn’t enough on its own, or is not practical, such as when a retrofit is required. It is also worth noting that when insulation is added underneath, the slab is considered ‘engineered’ and therefore requires an engineer to sign off. For these reasons, perimeter insulation is also often used instead or as well.
Perimeter Insulation
A surprising amount of heat is lost through the perimeter of a concrete slab, as recognised in the latest R-value calculations. Adding perimeter insulation is an effective way to improve the thermal resistance of the slab. Perimeter insulation can be included insitu for new slabs, or added retrospectively for existing slabs.
Using insulation for edging on new slabs
The advantage of including in situ insulation for new slabs is that it can be positioned before the concrete is poured, removing the need to fit afterwards. The preference, in addition to installing a high performing product, is to make it as easy as possible to position the edging, manage the corners and finish with an effective result. Choosing an edging product that provides for all standard heights as well as bespoke heights, ensures the product will match up with the dimensions of the slab. It is also helpful to have premade corners to ensure a high-quality finish and to avoid gaps developing over time.
In our drive to deliver the best solutions to the market, EXPOL have collaborated with concrete slab experts, MAXRaft to deliver a new solution. EXPOL MAXEdge is a high-performance slab edge insulation system. It is designed for the Kiwi market, to meet the new H1 standards. It comes with a coated and uncoated finish. The pre-made L shaped perimeter insulation fits easily inside the slab framework. With a variety of standard and bespoke heights, and premade corners, it is suitable for any frame size.
Why use a coated edging?
One of the issues with adding insulation to the edge of the concrete slab, is the additional time and expense it brings. The slab itself requires no finishing, but by adding insulation, additional plastering and painting is required. To minimise this, EXPOL edging comes with the option of a water-proof resin coating that doesn’t require painting. This removes the need to plaster the edges after the pour, saving time, labour and material costs.
Retrofit
When retrofitting an existing slab, it’s ideal to use a product that can offer a high thermal resistance, and is also easy to adhere to the slab. EXPOL’s ThermaSlab Edge comes with a product R-value of 1.0. It is designed to fit under the external cladding and adhere to the concrete floor, giving a professional finish. The coated option provides the appearance of being part of the concrete slab, removing the need to plaster or paint it once you’ve applied it. EXPOL’s patch kit includes the water-based water-proof resin which is easy to apply to help manage joins or scratches.
How do I calculate the R-value for my concrete slab?
Choosing the right products takes on a whole new challenge when trying to meet the R-values required for new slabs as there are a number of variables to line up. The calculations for concrete slabs are relatively complex, taking into consideration the size of the slab, the area/perimeter ratio, the climate zone and the thermal performance of the insulation. In addition, each product has different R-values, and when you combine edging and underslab insulation, it adds another layer to an already tricky calculation.
The good news is that the team at EXPOL love getting stuck into the technical details as much as they love helping their customers. Our Technical Team has put together a comprehensive set of tables, along with a handy perimeter/area calculator to help you make light work of concrete slab R-values.
You can find the tables here.
- Simply use the online calculator to find out your area/perimeter ratio
- Match this to the R-value you require (based on your climate zone)
- Check the top of the column to find the combination of products needed to deliver it
The R-value tables are calculated in accordance with Verification Method H1/VM2 Appendix F.
If your requirements sit outside these tables, or you’d like some help with a , please contact us and we’ll happily help out.
We are really proud of our products, the engineering and research behind them, and the team that delivers them to you. Please reach out with any questions or suggestions, we love hearing from you.